Day :
- Advances in 3D Printing & Additive Manufacturing Technology | Innovations in 3D Printing | Design for 3D Printing | 3D Printing Materials | Benefits of 3D Printing and Technology | Future Technology in 3D Printing | Challenges in 3D Printing | 3D printing in Biomaterials | Clinical applications of 3D Printing Innovations | Applications of 3D Printing in healthcare & medicine | Nano 3D Printing
Location: Rome, Italy
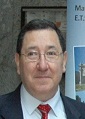
Chair
José L Ocaña
UPM Laser Centre - Polytechnic University of Madrid, Spain
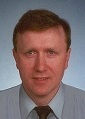
Co-Chair
Miroslav Piska
Brno University of Technology, Czech Republic
Session Introduction
Srdjan Milenkovic
IMDEA Materials Institute, Spain
Title: Development of Al alloys for additive manufacturing
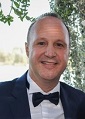
Biography:
Srdjan Milenkovic obtained a PhD in 2002 from the State University of Campinas, Brazil. He joined the Department of Materials Technology at the Max-Planck-Institute for Iron Research (MPIE) in Düsseldorf, Germany, as a Research Associate. Since March 2011, he was appointed as a Head of the Solidification Processing and Engineering group at the IMDEA Materials Institute. His research expertise includes advanced solidification processing techniques with special emphasis on gas atomization of powders for additive manufacturing and development of novel high- throughput casting methods. He has published over 55 papers in JCR journals, among which two in Nano Letters with impact factor >10.
Abstract:
Additive manufacturing (AM) technology is being adopted in more and more industries and the focus of research and development is shifting to the materials in use. However, limited processability of high-performance materials restrict the robustness of the process in some cases, while in other cases the best materials for a given application cannot be processed at all. Currently only a few alloys can be reliably processed by this methodology, and in particular the number of different aluminium alloys available for AM is still rather limited. The main reason is that the strongest Al alloys, which get their strength from precipitation hardening, contain highly volatile elements such as Zn, Mg, etc. leading to turbulent pools, pores and low mechanical properties. This talk will review ongoing research on development of the innovative aluminium alloy specifically designed for SLM. Two different approaches will be presented: on one hand, on tailoring the chemical composition to improve processability, specifically crack susceptibility, of wrought aluminium alloys of the 7xxx series (Al-Zn alloys) to increase mechanical resistance of weldable casting grade AlSi10Mg alloy. A special emphasis will be placed on powder production by gas atomization as a first and an important step in alloy development for additive manufacturing. It will be demonstrated how the desirable compositions can be achieved and what are the main challenges faced. Also the properties of the powders will be assessed and suitability for SLM demonstrated.
A Errachid
UMR 5280-Institut des Sciences Analytiques, CNRS, Université de Lyon, France
Title: A 3D-printed automated sample storage unit for sporadic sampling in innaccessible aquatic environment
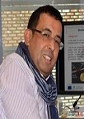
Biography:
A Errachid is a Full Professor Classe Exceptionnelle at the University Claude Bernard-Lyon 1 since the end of 2008. He received his PhD degree from the Universitat Autonoma de Barcelona in 1997. Between 1997 and 2001 he worked as Junior Research Scientist at the Centro National de microelectronica (CNM). He later joined the Department of Electronics of University of Barcelona and IBEC as Senior Research, where he worked from 2001 till 2008. He has obtained top-level results in the field of silicon-based (bio)chemical sensors using field-effect transistors and micro/nanoelectrode structures. His deep knowledge and understanding of the electronic devices structure as well as operation and interplay between (bio)chemical molecules and electronics, has resulted in development of novel (bio)sensor devices such as, the original nanosensor device based on olfactory proteins developed under SPOT-NOSED project, amongst others). He has an extensive expertise in EU projects coordination and participation, including KardiaTool (H2020-NMBP-X-KET-2017 no. 768686), HEARTEN (H2020-PHC-26-2014, no. 643694), MicroMole (H2020-FCT-2014, no. 653626), DiagCan (FP7-PEOPLE-2013-IEF, no. 628363), Sea-on-a-Chip (FP7-OCEAN-2013, no. 614168), SMARTCANCERSENS (ICT FP7, no. 294993), and SensorART (ICT-FP7, no, 248763) projects. To date, he has published more over than 195-refereed Scopus papers and his h-index is 28.
Abstract:
Sewage epidemiology has been proven to be a powerful tool to profile a community’s behaviour both in large and small areas. Conventional wastewater analysis is based on manually taken samples, subsequent transport to a specialized lab environment and analysis within a certain period of time. However, due to the high logistic efforts, sampling intervals are usually rather long and can hardly be carried out spontaneously or out of a well-planned sampling campaign. Therefore, automated sampling devices are becoming popular nowadays, as they can be placed on-site in a single operation and be in stand-by mode during long periods of times waiting to be triggered by a predefined sampling protocol. In this context, we report on a miniaturized, low-cost, easy-to-operate and low-power consumption microfluidic automated sampler for sporadic sample collection. The device uses a piezoelectric micropump and three miniaturized electro-valves that are assembled in a 3D-printed microfluidic manifold. Up to three samples can be stored in a 3D-printed single manifold that contains three 2.3 mL reservoirs connected to main body of the device. Moreover, the automated sampler can be remote controlled using a customized control board that enables to trigger the system and set a desired flow rate and time of sampling. Furthermore, its low-power- consumption feature enables the device to be powered through a lithium battery. All these qualities make the automated sample device to be very useful for applications where one or several sporadic samples must be taken in poor accessible environments such as the sewer network without the need of personal presence during the sampling event.
Martin Hannibal
University of Southern Denmark, Denmark
Title: Additive manufacturing in the manufacturing industry – use, developments, & potentials
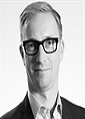
Biography:
Martin Hannibal is Head of Research in International Business & Entrepreneurship at the Department of Marketing & Management, SDU. His research is focused on knowledge intensive start-ups and additive manufacturing. He is actively involved in international research networks focused on these topics (Academy of International Business). He has published in various high ranking and topic specific peer-reviewed outlets such as International Business Review, Journal of International Marketing, Entrepreneurship & Regional Development, and Journal of International Entrepreneurship. He has been involved in several projects involving industrial partners and has a wide experience in disseminating and discussing research with relevant industrial partners.
Abstract:
Industry 4.0 is epitomized by several emerging technology breakthroughs and represent new ways in which technology becomes embedded within products, services, industries and societies in general. The evidence of dramatic changes caused by some of the constituent technologies of i4.0 such as additive manufacturing (AM) has already been illustrated through numerous business cases. Based on this many authors suggest that entire industries will be disrupted by AM. Many observers have argued that AM will offer numerous opportunities for existing firms and provide a basis for a new generation of start-up firms. The specifics of these opportunities and concrete potentials may be highly dependent on the specific industrial setting. However, empirical research into the details of this still very sparse. To address this gap in literature a survey has been conducted on Danish manufacturing firms. The survey tracked in which domain – prototyping, production support, or finished products – AM is currently used. Our research shows, a primary use of AM in prototyping and product development processes as well as a broad use in production support – grippers, fixtures, tools etc. Our research indicates that ownership coupled with multi-domain use of AM is a key driver to both business development in general and development of new products and services. The research indicates this potential of AM is not dependent on size of the firm implementing the technology.
Martin Hannibal
University of Southern Denmark, Denmark
Title: Additive manufacturing in the manufacturing industry – use, developments, & potentials
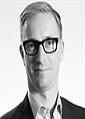
Biography:
Martin Hannibal is Head of Research in International Business & Entrepreneurship at the Department of Marketing & Management, SDU. His research is focused on knowledge intensive start-ups and additive manufacturing. He is actively involved in international research networks focused on these topics (Academy of International Business). He has published in various high ranking and topic specific peer-reviewed outlets such as International Business Review, Journal of International Marketing, Entrepreneurship & Regional Development, and Journal of International Entrepreneurship. He has been involved in several projects involving industrial partners and has a wide experience in disseminating and discussing research with relevant industrial partners.
Abstract:
Industry 4.0 is epitomized by several emerging technology breakthroughs and represent new ways in which technology becomes embedded within products, services, industries and societies in general. The evidence of dramatic changes caused by some of the constituent technologies of i4.0 such as additive manufacturing (AM) has already been illustrated through numerous business cases. Based on this many authors suggest that entire industries will be disrupted by AM. Many observers have argued that AM will offer numerous opportunities for existing firms and provide a basis for a new generation of start-up firms. The specifics of these opportunities and concrete potentials may be highly dependent on the specific industrial setting. However, empirical research into the details of this still very sparse. To address this gap in literature a survey has been conducted on Danish manufacturing firms. The survey tracked in which domain – prototyping, production support, or finished products – AM is currently used. Our research shows, a primary use of AM in prototyping and product development processes as well as a broad use in production support – grippers, fixtures, tools etc. Our research indicates that ownership coupled with multi-domain use of AM is a key driver to both business development in general and development of new products and services. The research indicates this potential of AM is not dependent on size of the firm implementing the technology.
Andrew J Kobets
Children's Hospital at Montefiore, USA
Title: Virtual modeling, stereolithography, and intraoperative CT guidance for the optimization of sagittal synostosis reconstruction
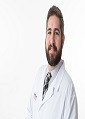
Biography:
Andrew J Kobets is currently Chief Resident of Neurosurgical Resident at Montefiore Medical Center and is working on a translational research project as a Visiting Scientist at both the Feinstein Institute for Medical Research at Northwell Health and at the Albert Einstein College of Medicine. He has initiated and overseen the initiation of three clinical trials in the Department of Neurological Surgery at Montefiore Medical Center and is the first utilizing MR Elastography to evaluation shunt function in New York. He graduated from the Yale School of Medicine with a medical degree and a Master’s in Health Sciences. He studied Systems Neuroscience at the Johns Hopkins University as an Undergraduate and will return to Johns Hopkins after residency for a Fellowship in Pediatric Neurosurgery.
Abstract:
Objective: Sagittal synostosis affects 1 in 1000 live births and may result in increased intracranial pressure, hindrance of normal neural development, and cosmetic deformity due to scaphocephaly. Historically, several approaches have been utilized for surgical correction and recently, computed tomography (CT)-guided reconstruction procedures are increasingly used. In this report, the authors describe the use of a CT-derived virtual and stereolithographic (3D printed) craniofacial models, which are used to guide intraoperative bone placement, and intraoperative CT guidance for confirmation of bone placement, to ensure the accuracy of surgical correction of scaphocephaly, as demonstrated to parents.
Methods: Preoperative high-resolution CT imaging was used to construct 3D image sets of the skulls of two infants (a 14-month-old female and a 6-month-old male) with scaphocephaly. These 3D image sets were then used to create a virtual model of the proposed surgical correction for each of the infants’ deformities, which was then printed and made available for use intra-operatively to plan the bone flap, fashion the bone cuts, and optimize graft placement. After the remodeling, adherence to the preoperative plan was assessed by overlaying a CT scan of the remodeled skull with the virtual model. Deviations from the preoperative model were noted.
Findings: Both patients had excellent postoperative cosmetic correction of head shape and contouring. The mean operative time was 5 h, blood loss was 100 ml, and one child required modification of the subocciput after intraoperative imaging showed a deviation of the reconstruction from the surgical goal as depicted by the preoperative model.
Conclusion: The addition of neuro-navigation to stereolithographic modeling ensured the accuracy of the reconstruction for our patients and provided greater confidence to both surgeons and parents. While unisutural cases are presented for clarity, correction was still required for one patient. The cost of the models and the additional CT required must be weighed against the complexity of the procedure and possibly reserved for patients with potentially complicated corrections.
Konrad Gruber
Wrocław University of Science & Technology, Poland
Title: The methodology of selective laser melting process development
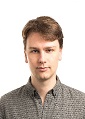
Biography:
Abstract:
Nowadays trends on manufacturing technologies market, as well as growing requirements especially from the specialist industry such as aviation, create new challenges for designers and producers, which result in the necessity of modifying properties of materials and structural components. One of the possibilities to influence these properties is application of additive technologies (e.g. selective laser melting - SLM) for production of prototype models, pre-production and production series, finished products, possibly with internal spatial structures, which in a significant way change tribological properties, resistance to mechanical loads, operational durability, as well as resistance to unfavorable and hard working conditions. The essential factors determining the definition of a given technology as the future-oriented and worth of developing are the achieved features of the worked shapes and surfaces, costs of its implementation and use, elasticity and care for the natural environment. SLM is a fast growing technology, which creates opportunities for manufacturing complex geometries (both monolithic volumes and spatial structures) directly from metal powders and CAD 3D models. Therefore, the SLM technology is recognized as a manufacturing technology of the future. Many industry leaders are implementing SLM into their production standards, e.g.: automotive, aviation, space and medicine companies. SLM technology can also be used for the development of new materials, through the possibility of manufacturing elements from various mixtures of metal powders. The methodology presented in this article allows expanding the use of SLM in a wide range of industries and tests the properties of new materials on functional parts and 3D specimens.
Patrycja Szymczyk
Wrocław University of Science & Technology, Poland
Title: Additive manufacturing of porous structures for medical applications
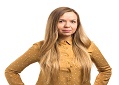
Biography:
Patrycja Szymczyk received her PhD (2015) degree from the Wrocław University of Science and Technology. She is an Assistant Professor at the Faculty of Mechanical Engineering of WrUST. Her current research interests are related to medical applications of AM technologies and includes the design, manufacturing and testing of advanced biomedical objects, such as biomechanical functional structures (BFS) for tissue regeneration, custom-made implants and smart drugs delivery systems for a wide spectrum of materials dedicated to the medical and pharmaceutical industry.
Abstract:
The development of modern medicine is possible through extensive cooperation of interdisciplinary teams, bringing the latest achievements in many fields of science, to implement new methods, materials and technologies. Regeneration of large tissue defects caused by tumour resection or lost as a result of accidents is one many challenges faced by surgeons. Individualized (custom-made) implants, shape-fitting patients’ anatomies, are now easier to obtain thanks to modern computerised technologies, such as additive manufacturing (AM). Advanced 3D-printed implants eliminate the need for traditional treatments utilising autogenous one transplants with additional surgery site or conventional implants, and lower the risk of infections or implant loosening due to incomplete geometric adjustment. One of the main advantages of additive manufacturing is in fact the capability of producing objects with complex geometries and varying mechanical parameters in their different zones. Bone-replacement biomechanical functional structures (BFS) with diversified structure may be used to fill bone defects resulting from injuries or diseases and offer an effective method of counteracting existing dysfunctions of a patient. Designing and manufacturing of BFS structures for medical applications is an innovative and interdisciplinary issue, which becomes more and more popular but requires further research and development.
Marina Cabrini
University of Bergamo, Italy
Title: Corrosion behavior of metallic alloys obtained by additive manufacturing
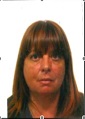
Biography:
Marina Cabrini is an Associate Professor of metallic materials, polymer, composites and ceramics, and biomaterials at the University of Bergamo and of PhD course in Electrochemistry and Electrochemical Technologies. She is an Italian delegate in the Board of International Corrosion Council (ICC), member of European Federation of Corrosion and International Electrochemical Society. Her research activity is on electrochemistry and corrosion, primary focused on the environmental assisted cracking of traditional and innovative alloys, biomaterials, and corrosion of alloys produced by means of additive manufacturing. She has published more than 40 papers in reputed journals and has been serving as Review and Editorial Board Member of repute journals.
Abstract:
Among the alloys, the most used in additive manufacturing (AM) technologies are surely Co-Cr, Ti-, Al- and Ni-alloys. Such alloys cover the most widespread industrial applications form automotive/aerospace, to medical, energy and oil & gas. The material qualification process of the alloys in the specific environment is nowadays gaining lot of importance, as the corrosion behavior of traditional casting and wrought alloys is well known, but it significantly modifies due to macro and microstructure modifications induced by additive manufacturing process. The results of several reserches emphasize strict correlation between the corrosion behavior and the unique microstructure of these alloys, thus giving rise to new opportunities for increasing the knowlwge in corrosion science. Corrosion mechanisms are also affected by both the production processes and heat treatments. Additive technologies have several and undubtful advantages compared to subtractive ones, mainly due to the possibility to produce components with very complex and non-dense geometries (micro and macro porous, trabecular, etc.). The unique microstructure, the widening of the solubility field of the alloy elements due to rapid cooling, the precipitation of non-equilibrium phases, the different surface conditions and heat treatments are only some of the elements affecting both the mechanical behaviour and the corrosion resistance. In fact, for applications in particularly aggressive environments, the qualification of these materials must be completely re-discussed, as well as the definition of new production standards and post-processing heat treatments specifically designed to enhance their peculiarities.
Teresa Russo
Institute of Polymers, Composites and Biomaterials - CNR, Italy
Title: Multifuncional materials and additive manufacturing for healthcare
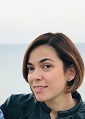
Biography:
Teresa Russo obtained a PhD in Materials and Structures Engineering (Biomaterials) at the University of Naples, Italy. She is as a Researcher of the Institute of Polymers, Composites and Biomaterials (IPCB) – National Research Council of Italy – and her work is mainly focused on the possibility to combine additive manufacturing technologies, electrofluidodynamic techniques and multifunctional injectable gels for the optimization of multifunctional devices for tissue repair and regeneration. She is currently author of national and international papers, different book chapter and communications in international and national conferences. She has also been serving as an Editorial Board Member of repute journals.
Abstract:
Over the past years, porous bioactive scaffolds with controlled functionalities, obtained via additive manufacturing of polymer-based compounds have attracted research interest in the field of tissue repair and regeneration. On the other hand, the design and the application of injectable systems and hydrogel-based composites able to promote the regeneration of soft tissues represents a crucial aspect for damaged tissue repair, also considering that such strategies could be used in reducing surgical invasiveness and in enhancing biomolecular interactions with cells. Furthermore, in order to repair bone, cartilage, intervertebral disc, adipose tissue, neural, and cardiac tissue, hydrogel-based materials have been widely analyzed as cell delivery systems providing a controlled release of drugs, proteins, cells, gene and other immobilized biomolecules. The suitable combination of 3D scaffold and hydrogels could provide high performance and functional systems, also focusing the attention on the possibility to control drugs or bioactive agent release. In this scenario, 3D polymeric and composite rapid prototyped scaffolds were properly designed and developed, by means of rapid prototyping technique. Different formulation of collagen and collagen-low molecular weight hyaluronic acid (LMWHA) were selected and combined with 3D scaffolds. The biological and chemico-physical performances of the proposed devices have been assessed. On the other hand, rheological and injectability tests were performed in order to obtain important information on the functional properties of the injectable systems in terms of viscoelasticity and flow behavior.
Maredi E
IRCCS Rizzoli Orthopaedic Institute, Italy
Title: The use of 3D models in the pre-operative evaluation of the treatment of the foot congenital flat foot
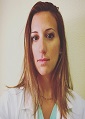
Biography:
Maredi E has complted her degree at School of Medicine in Bologna Italy and Specialization in Orthopedics with full marks. She works at the paediatric orthopedics department of the Rizzoli orthopedic institute. Author of numerous publications in the paediatric and vertebral field, such as Surgical treatment for scoliosis associated with rare disease and Neurofibromatosis type I and multiple myeloma coexistence: A possible link? she has participated in numerous courses and conferences as a speaker or learner. Winner abstract for young category at the Italian Scoliosis Group (GIS). The major field of application at the moment is the paediatric deformity from the spine to the foot.
Abstract:
The flat foot is a complex multi-planar deformity from the leveling of the longitudinal plantar vault of the foot. From 2016 to 2017, 62 feet affected by tarsal synostosis. Of these 62 feet, for 26 we required a 3D model to be able to study preoperatively, 2 of which to be used directly on the operative field, after sterilization. Then we evaluated and compared between the 2 groups, in patients who had at least 12 months of follow-up: operative time, intraoperative complications, extra-operative complications, pain and return to daily activity / sport, surgical time and satisfaction of the surgeon. The obtained data, collected at a mean follow-up of 14 months (min 12, max 30), do not show an improvement of the clinical condition, expressed as pain (VAS without 3d: 9; VAS with 3d: 9) and recovery of sport activity (FADI/FAAM without 3d: 91%, with 3d: 89%). Also the extra-operative complications, such as infections, deformity in persistent flatness or breaking of the synthesis media, are unchanged in the two groups (without 3d: 2/36 - 5%, with 3d: 1/25 - 4%). An improvement was however obtained in the reduction of the operative time, with a decrease of 10 min of intervention mean (without 3D: 55 min of average, with 3D: 45 min of average) and of those that are intraoperative complications (without 3D: 8%, with 3d: 3%). The satisfaction of the surgeon, assessed with specific satisfactory survey showed a clear satisfaction in the use of 3D models, thanks to which it was possible to isolate the synostosis in a shorter time and a more rapid resection of the same. The creation of 3D models (scale1:1) of the pathology is decisive in the planning of a better surgical strategy for the patient, in the calculation of the size of the synostosis and in the implementation of specific cutting guides for the patient. All this translates into a shorter surgical and infectious risk of the patient, with also good signs of satisfaction of the surgeon.
- 3D Printing Industries | 3D Image Processing and Visualization | 3D printing technology and innovations | Metal 3D Printing | Polymers in 3d printing | 3D Bio printing | Lasers in 3D Printing in Manufacturing Industry | 3D Printing of Supply Chain Management | Tissue and Organ Printing | 3D Printing Technology Impact on Manufacturing Industry
Location: Rome, Italy
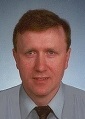
Chair
Miroslav Piska
Brno University of Technology, Czech Republic
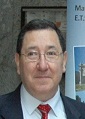
Co-Chair
José L Ocaña
UPM Laser Centre - Polytechnic University of Madrid, Spain
Session Introduction
Arnautov A
NUST “MISiSâ€, Russia
Title: Selective laser melting of aluminum matrix composites with ceramic fillers
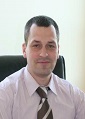
Biography:
Arnautov A is now at the completion of his PhD from the research group of Prof. Dr.-Ing. Alexander Gromov, NUST “MISiS” University, Moscow. He is the Head of the Department at RUSAL Co., a premier research organization. He has published more than 10 papers in reputed journals and conference proceeding on additive manufacturing.
Abstract:
3D printed aluminum details are lightweight (density 2700 kg/m3) and moldable, having an elasticity modulus of ~70 MPa. These are the main requirements of the 3D printing industry. However, aluminum is not strong or hard enough: the tensile strength even for the duralumin alloy is ~500 MPa, and its hardness HB sits at 20 kgf/mm2. The developed modifying precursors for aluminum matrix composites (AMC), based on aluminum nitrides and oxides obtained through combustion or hydrothermal/dry Al oxidation, have become the basis of the new composite. We develop a technology to strengthen the AMC obtained by 3D printing, and we have obtained innovative precursor-modifiers. Combustion or oxidation products - aluminum nitrides and oxides - are specifically prepared for sintering branched surfaces with transition nanolayers formed between the particles. It is the special properties and structure of the surface that allows the particles to be firmly attached to the aluminum matrix and, as a result, increase the strength of the obtained composites.
Krzysztof Kanawka
Blue Dot Solutions, Poland
Title: Use of additive manufacturing technology for fabrication of lattice structures via SLS method in
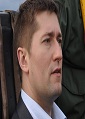
Biography:
Krzysztof Kanawka, PhD DIC, serves as CEO of a Polish space sector company Blue Dot Solutions. The company is active in fields such as practical use of satellite data, space markets (especially in Europe) and mechanical engineering. In the past Krzysztof Kanawka studied at the Department of Chemical Engineering at Imperial College London, where he did PhD in the field of (cermet) Solid Oxide Fuel Cells.
Abstract:
This abstract summarises the project named “Development of a multifunctional case for aerospace electronics, which special focus on power electronics and power supply”. This project was realised by the Blue Dot Solutions company and co-financed by the (Polish) National Research And Development Centre.
Several different types of lattice materials fabricated via the SLS method were designed and examined. Initially, these structures were simulated, a then were sintered via the SLS method. The material used for this project was “Alumide”, whic is a 7:3 mix of PA12 polyamid and aluminium. The main properties of this metallic-looking material are: high stiffness and very good characteristics for post-processing. Pieces of Alumide materials can undergo various post- treatment techniques, such as sanding, polishing or grinding.
Studies and numerical simulations were done on several basic isotropic cells. Five of them were analysed further: 1e, 1f, 1h, 2b, 5 (il. 1).
The goal of the analisis was to determine the equivalent of thickness in dependence to structure of a single cell. The numerical analysis was done for thermal and thermodynamical cases (il. 2).
Sahar Sultan
Stockholm University, Sweden
Title: 3D printed porous bioscaffolds based on cellulose nanocrystals
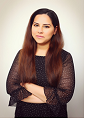
Biography:
Sahar Sultan is a third year PhD student in Stockholm University. She is actively working with 3D printing of cellulose nanoparticles. She has also served industry for 5 years by working as a researcher and safety officer in a solar cell company called Exeger Sweden AB.
Abstract:
Nanocellulose extracted from natural resources are used extensively in biomedical field. They have properties of cellulose, such as potential for chemical modification, low toxicity, biocompatibility, biodegradability, low toxicity, high mechanical properties, renewability as well as nanoscale characteristics like high specific surface area, rheological and optical properties. Due to the inherent shear thinning property of nanocellulose, the 3-Dimensional (3D) printing technique has revolutionized the bioscaffolds with customization, complex geometries, controlled porosity, bioprinting and hierarchical features, in terms of composition and structural designs. Furthermore, during 3D printing the high aspect ratio of cellulose nanocrystals (CNCs) is expected to induce shear alignment yielding directionality in the 3D printed scaffolds. CNCs based double crosslinked interpenetrating polymer network (IPN) hydrogel has been made and 3D printed into 2D and 3D scaffolds with uniform and gradient porosity. The pore sizes are in the range of 80-2080 µm and 195-2382 µm in the wet and freeze-dried states respectively. These pores are distributed in a controlled manner that in turn provides gradation in density and porosity of the 3D printed hydrogel scaffolds. The directionality studies showed that CNCs tend to align parallel to the printing direction and degree of orientation varies between 61-76 %, depending on the point of measurement within the 3D printed scaffolds. In addition, this study also highlights the importance of nozzle movement during 3D printing to achieve scaffolds with better resolution, higher dimensions and good shape fidelity. The alignment of nanocrystals in this work yields directionality that can serve as an important step toward the development of tailored architectures. This study demonstrates the potential of 3D printing in developing bio-based scaffolds with controlled pore sizes, gradient pore structures and customized geometry for optimal tissue regeneration applications.
Seong-Woo Woo
Reliability Association of Korea, South Korea
Title: Reliability design of mechanical systems subject to repetitive stresses
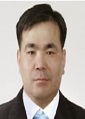
Biography:
Seong-Woo Woo has a BS and MS in Mechanical Engineering, and he has obtained PhD in Mechanical Engineering from Texas A&M University. He major in energy system such as HVAC and its heat transfer, optimal design and control of refrigerator, reliability design of thermal components, and failure Analysis of thermal components in marketplace using the non-destructive such as SEM & X-ray. He worked in Agency for Defense Development, Chinhae, South Korea, where he was Researcher in Charge of Development of Naval Weapon System. Now he is working as a Senior Reliability Engineer in Side-by-Side Refrigerator Division, Digital Appliance, Samsung Electronics, and focus on enhancing the life of refrigerator as using the accelerating life testing. He also has experience about side-by-side refrigerator design for best buy, Lowe’s, cabinet-depth refrigerator design for general electrics.
Abstract:
The basic reliability concepts - parametric ALT plan, failure mechanism and design, acceleration factor, and sample size equation were used in the development of a parametric accelerated life testing method to assess the reliability quantitative test specifications (RQ) of mechanical systems subjected to repetitive stresses. To calculate the accelerâ–ºation factor of the mechanical system, a generalized life-stress failure model with a new effort concept was derived and recommended. The new sample size equation with the acceleration factor also enabled the parametric ALT to quickly evaluate the expected lifetime. This new parametric ALT should help an engineer uncover the design parameters affecting reliability during the design process of the mechanical system. Consequently, it should help companies improve product reliability and avoid recalls due to the product failures in the field. As the improper design parameters in the design phase are experimentally identified by this new reliability design method and recent patents are addressed, the mechanical system should improve in reliability as measured by the increase in lifetime, LB, and the reduction in failure rate, l.
Farhang Momeni
University of Michigan-Ann Arbor, USA
Title: 4D printers: integration of multi-material additive manufacturing with intelligent heads to predict the fourth dimension
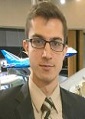
Biography:
Farhang Momeni received his BS in Aerospace Engineering from the Sharif University of Technology in 2014. He finished his BS in three years rather than the usual four years (Sep 2011-Sep 2014), while he was ranked 1st among all B.S. students in Aerospace Engineering at the Sharif University of Technology that graduated in 2014. He published two journal articles in Thermodynamics before his B.S. graduation date. Then, in 2015, he received Direct Ph.D. admission with fellowship award from the Mechanical Engineering department at the University of Michigan-Ann Arbor, where he obtained his M.S. and Ph.D. in 2017 and 2018, respectively.
Abstract:
3D printing is a relatively known manufacturing process and the inimitable features provided by 3D printing (such as complexity-free geometry and material saving) are also well-known. Similarly, 4D printing should be explicitly underpinned as a novel manufacturing technology and the unique traits empowered by 4D printing should be elucidated too. 4D printing was initially defined as a combination of shape memory materials and additive manufacturing. In our recent review paper, I illustrated the differences between 3D and 4D printing. In addition to smart (not necessarily shape memory) materials and additive manufacturing, “4D printing mathematics” is also required to yield a “4D printed” structure. Furthermore, unlike 3D printers, 4D printers are not available and the 4D printing process is currently accomplished by existing 3D printers in a passive manner. The phrase “4D printer” was used in the related literature. However, I need to clarify that; “4D printer” is not truly established by converting a single-material printer into a multi-material printer, or by incorporating different additive manufacturing methods into one printer. I should add that a “4D printer” must be capable of investigating and predicting the “4th D”. Consequently, an “intelligent head” should be constructed and integrated with present multi-material printers. In this plenary talk, I will underpin 4D printing as a novel manufacturing paradigm, illuminate its unique features, and particularly prove its energy-saving feature by deriving its minimum energy consumption limit. Finally, I will embody future 4D printers and their connections to our laws of 4D printing.