Day 1 :
Keynote Forum
Alexander V Manzhirov
Ishlinsky Institute for Problems in Mechanics - RAS, Russia
Keynote: What is inside AM fabricated parts? the nature of residual stresses and shape distortion
Time : 09:30-10:10

Biography:
Prof. Manzhirov is a well-recognized scientist working in the field of mechanics and applied mathematics. Currently he is Deputy Director of the Ishlinsky Institute for Problems in Mechanics of the Russian Academy of Sciences and Head of the Department for Modeling in Solid Mechanics at the same institute. He is the author of more than 250 scientific publications, including sixteen books and four textbooks. His main scientific activities concern mechanics of growing solids, additive manufacturing technologies, contact mechanics and tribology, viscoelasticity and creep theory. He is also universally known as an author of the world’s first fundamental handbooks on integral equations.
Abstract:
Additive Manufacturing (AM) technologies are an exciting area of the modern industrial revolution and have applications in instrumentation, engineering, medicine, electronics, aerospace industry, and other fields. They include stereolithography, electrolytic deposition, thermal and laser-based 3D printing, 3D-IC fabrication technologies, etc. and are booming nowadays owing to their ability to fabricate products with unique characteristics that cannot be made with traditional fabrication techniques. AM enables cost-effective production of customized geometry and parts by direct fabrication from 3D data and mathematical models. However, to further the progress in the emerging area and empower scientists, engineers, and designers to fully implement the novel processes' capabilities, there is a need for a systematic study of mechanical analysis for AM technologies. Despite much progress in the area of AM technologies, problems of mechanical design and analysis for AM fabricated parts yet remain to be solved. So far, three main problems can be isolated: (i) the onset of residual stresses, which inevitably occur in the manufacturing process and can lead to failure of the parts, (ii) the distortion of the final shape of AM fabricated parts, and (iii) the development of technical and technological solutions aimed at improving existing AM technologies and creating new ones. We propose a fundamental approach for the modeling of surface growth of solids, which effectively describes the deformation processes in AM fabricated parts, as well as analytical and numerical methods for its implementation. This material is based upon work financially supported by the Russian Science Foundation under Grant No. 17-19-01257.
Keynote Forum
Frederic Dumur
Aix Marseille University, France
Keynote: Iodonium based photoinitiators: Towards simplified photocurable formulations

Biography:
Frederic Dumur has completed his PhD from Angers University (France) in 2002. From 2003 to 2008, he was successively a Postdoctoral Fellow in the group of Professor Ben L. Feringa (2003-2005), Nobel Prize 2016, Dr. Norbert Hoffmann (Reims, France), and Professor Francis Sécheresse (Versailles, France). Since 2008, he is Associate Professor at the Institute of Radical Chemistry of Aix Marseille University. He has published more than 180 papers in international journals. Frédéric Dumur is specialized in the design of organocatalysts and metal complexes as photoinitiators of polymerization under soft irradiation conditions.
Abstract:
Light induced cationic polymerization (CP) and free radical polymerization (FRP) reactions in the presence of a photoinitiator (PI) have been largely encountered for a long time in the radiation curing area. Today, due to their decisive advantages (low heat generation, low energy consumption, low operating costs, less maintenance, long life, portability, compact design, easy and safe handling, possible incorporation in robots or 3D printers, etc.), many developments are related to the use of Light Emitting Diode (LED) arrangements as excitation sources instead of the traditional mercury lamps or even lasers. Particularly, applications in the violet spectral range require LEDs operating at 365, 385, 395 or 405 nm. One of the key points is still the matching between the PI absorption and the LED emission spectrum. This condition is easily fulfilled with a lot of radical PIs.
Diaryliodonium and triarylsulfonium salts and others have been extensively studied as PIs. However, the starting structures are characterized by an absorption in the UV region (230–300 nm). The design of novel high-performance cationic PIs directly adapted to violet or visible LED irradiation is still challenging. Here, we present a novel photosensitive iodonium salt resulting from a coupling between naphthalimide and diphenyliodonium moieties (Figure 1) being able to work under LED exposure at 365, 385 and 395 nm without any additive and to initiate the cationic polymerization of diepoxides, divinylethers as well as diepoxide/divinyether blends and also the FRP of methacrylates.
Keynote Forum
Gremillard Laurent
MATEIS (UMR CNRS 5510), France
Keynote: Robocasting of dense ceramic parts
Time : 11:05-11:45

Biography:
L. Gremillard has completed his engineering degree and PhD from INSA-Lyon. After a 2-years post-doctoral fellowship at Lawrence Berkeley National Laboratory, he was appointed a scientist at CNRS (France) in the Materials Science and Engineering Laboratory (MATEIS) at INSA-Lyon. He is now Senior Researcher at CNRS, and head of the Biological Interactions and Biomaterials team of MATEIS. He is mostly known for his work on zirconia as a biomaterial. He has published more than 65 papers in reputed peer-reviewed, international journals and has been serving as a symposium organiser of ESB2016 and EUROMAT 2017.
Abstract:
Additive manufacturing of ceramic has known a large expansion over the past few years, mostly for its ability for creating 3D complex ceramic bodies with controlled porosity. Robocasting, or direct-ink writing, is one of the techniques available for ceramic additive manufacturing. It implies the extrusion through a nozzle of a self-setting paste in the shape of a filament to create the desired shape, layer by layer. One of the great interests of this technique is the possibility to fabricate multimaterials in one single printing step, using multiple pastes. This include both porouse, architecture pieces and dense bodies. However, shaping dense bodies (from either single or multiple inks) is still a challenge not completely met by additive manufacturing in general and direct ink writing in particular, since the properties obtained by conventional processing have not yet been successfully reproduced.
The aim of this presentation is to demonstrate the correlation between printing parameters (nozzle diometer, inter-filaments distance, printing velocity, environment…), paste fabrication (solid loading, binder, solvent, mixing, degassing, rheology…), thermal treatments (drying, debinding), defects distribution and mechanical properties in final sintered bodies.
We’ll show that printing precision, pattern design, layer-to-layer spacing and substrate adhesion play a critical role on the quality of the final piece, in a way that is far more important for ceramics than for polymers and metals. An optimization of all steps of the robocasting process enables the fabrication of dense high-strength materials with mechanical properties similar to those obtained by conventional processing.
- Advances in 3D Printing & Additive Manufacturing Technology | Innovations in 3D Printing | Design for 3D Printing | 3D Printing Materials | Benefits of 3D Printing and Technology | Future Technology in 3D Printing | Challenges in 3D Printing | 3D printing in Biomaterials | Clinical applications of 3D Printing Innovations | Applications of 3D Printing in healthcare & medicine

Chair
Alexander V. Manzhirov
Ishlinsky Institute for Problems in Mechanics - RAS, Russia
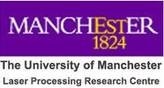
Co-Chair
Lin Li
The University of Manchester, UK

Biography:
Im a value Engineering Trainer and have been VE practice in 10 years, In relation to cost planning in particular, I took initiative in increasing profitability by coordinating target value in the procurement, design, and production technology departments, providing a list of items for cost reduction, and managing their progress.
Abstract:
This presentation introduces two specific approaches regarding the VE method - Benchmarking VE and Drawing VE.
I have been concerned about how to come up with good ideas effectively. I have used various methods by trial and error in idea generation sessions. By doing so, I noticed two methods proved to be effective. One is Benchmarking VE . It is used at the early development stage in order to coordinate the relationship between function and parts. Further, by applying this method to your competitors function and parts, you are able to ascertain the strengths and weaknesses of your company. and you can think good idea from comparison contents.
The other is Drawing VE. It can be used before, during, and after production. Specifically, it reexamines the role of the instructions in the drawing (materials, dimensional tolerance, function of thickness, thickness of the board, post-processing). And you can think cost reduction idea from reexamines the role of the instructions in the drawing .Based on this, the method allows you to develop new solutions.
I hope to share these methods with other VE practitioners around the world in order to contribute to the promotion of VE.

Biography:
Ikuo Yamamoto is a Professor of Nagasaki University.He worked in Mitsubishi Heavy Industries Ltd., JAMSTEC,and Professor at Kyushu,Kitakyushu,and Nagasaki University.He was leader of AUV “Urashima”,which established the world record for autonomous cruising;developed “Kaiko&Seabot”,which was crowned champion remotely operated vehicle at 10000m depth cruising and at the World convention 2012,2014,2016 and his robotic fish ‘swam’ in the International Space Station in 2009.He firstly sucessfully flied multi-rotor flight robotics with real-time monitoring and environmental sensor systems in Japan, 2008.
International Awards for developing medical robotics in 2014 and 2015. He is nominated as GlobalScot,Scotland Government, UK in 2017.
Abstract:
3D printers are useful for seamless development of robotics.The author uses 3D printer for making parts of robotics. Specilally,in the area of manufacturing surgical instruments, the ability to rapidly design, prototype, and test surgical instruments is critical. A case study of the rapid development of two biomechanism-based surgical instruments which are ergonomic and aesthetic are mentioned.It is designed, prototyped and conceptually tested in a short period of time by using 3D printer.Recently, there has been an increasing need for surgical instruments that can hold organs delicately yet stably. Such an instrument increases the efficiency of surgical operations by decreasing the physical and mental strain on both surgeons and patients. New biomechanism-based surgical instruments, based in part on the anatomical structure of a fish, provide soft-handling forceps where pressure is distributed over a larger area. The author created a seamless design method and prototyping process. This process has been used to prototype biologically-based mechanisms using 3-D CAD and a 3-D printer. Specifically, a fish-based mechanism which produces an elastic oscillating fin and shark skin which effectively controls hydrodynamic resistance have been found to be effective in creating superior surgical instruments. Developed user-friendly surgical instruments enable more efficient surgery,for example,50 percent reduction of surgical operating time. This process is effectively facilitated using a more seamless design through to the prototyping. Rapid manufacturing by 3D printer is important to check product in advancer.
Devi K. Kalla
Metropolitan State University of Denver, USA
Title: Functionally graded materials obtained by additive manufacturing technology

Biography:
Devi K. Kalla received a Ph.D. in industrial engineering from Wichita State University. He is currently an Associate Professor in the Department of Mechanical Engineering Technology at Metropolitan State University of Denver. He has a strong experience on composite manufacturing, 3D prining, and modeling. He has published more than 25 papers in reputed journals and conference proceedings and has been serving as an editorial board member of International Journal of Material Sciences and Technology (IJMST), International Journal of Industrial Engineering and Technology (IJIET) and more notably, as the Editor-in-Chief of the International Journal of Mechanical and Material Sciences Research (IJMMSR).
Abstract:
In the current study, Direct Metal Laser Sintering and Binder Jetting technologies are employed for direct manufacturing of functionally graded materials. In the past, the additive manufacturing approach has been limited to non- functional parts and their repair. In this project, we are extending this technology to functional graded gears through design decomposition, process modeling and smart machines. This project aims at developing functionally graded material (FGM) manufacturing technologies that enable creation of light weight “Net Shape” parts for power transmissions used in multiple markets such as transportation and power generation. The technologies include design decomposition, additive manufacturing and material characterization. This transformational approach will enable sustainable manufacturing through reduction in material use, processing steps, energy consumption and carbon footprint and create products which have better performance characteristics. Additive manufacturing technology may provide an efficient alternative way to fabricate customized dental implants based on a CAD file with a functionally graded structure that may minimize stress shielding and improve the long-term performance of dental implants.

Biography:
Xipeng Xu is President of Huaqiao University. He has his expertise in machining technology and functional usage of diamond materials. He is executive member of International Committee for Abrasive Technology (ICAT) and gets over 140 technical papers publication in related journals and conference.
Abstract:
In this paper, a practice to fabricate ultraviolet (UV) cured resin bond grinding wheels with abrasive grits in controllable 3-dimensional (3D) distributions was reported. The challenge in fabrication of resin-bonded grinding wheels with controllable abrasive girts distribution is to simultaneously cure heterogeneous materials with suitable slice thickness and sufficient bonding strength between cured layers. This is beyond the capability of most commercially available 3D printers. A new Stereolithography Apparatus equipment with automatic functions of resin applying, grits planting, resin curing and wheel lifting was developed. Successively, multi-layered abrasive wheels were fabricated by planting abrasive grits and UV curing resin layer-by-layer. In doing so, 3D grinding wheel with controllable abrasive girts distribution were fabricated. Finally, the grinding performance and wear characteristics of newly developed grinding wheels were revealed through the grinding experiments. The results indicated that the distribution of diamond abrasive grits plays a determining role in the wear behavior, and hence the grinding performance of resin grinding wheels has been greatly improved.
Pinlian Han
South University Of Science And Technology, China
Title: How far we can go to print a jet engine? The beauty of a 3D printed micro jet engine

Biography:
Graduated with BSc and MSc from Xian Jiaotong University in China, another two MSc degrees in USA and one PhD degree in Canada, worked at Pratt & Whitney Aero Engine Company in USA for more than 12 years as technical leader at 7 different departments. Published over 70 papers and more than 50 patents. Currently a Chair professor in the Department of Mechanics and Aerospace Engineering, leading a team to break through the bolt neck of aero engine with innovative technology and methodology, focusing on additive design and developing a new type of aero engine called Amphibious Relay Gas Turbine.
Abstract:
Additive manufacturing (AM) opens a new era, including aircraft engine design and manufacturing. In addition to being capable of solving problems with complex shapes that are difficult to make with traditional methods, the revolutionary power of AM is due to the feature of making objects from micro to macro scale, similar to natural processes such as how living beings grow from small to large. Now one can put different materials together where needed, either mixed or embedded. One can proactively design micro structure under the surface of a structure to arrange distribution of mass, stiffness, damping, failure mode and its location, thermal property, etc., according to the functional requirement of the part. This is what we call Additive Design (AD), not design for AM. AD will be a new area of engineering that will change people's vision of design and lead to exploring the further capabilities of existing materials by optimizing the load distribution, such as reducing stress concentration substantially.
We made a micro jet engine in 3 months using AD technology developed by a small group with young people of less than 10 members. From inlet to the tail nozzle, all parts are made of metal using SLM by outsourcing to different companies. The entire engine consists of no more than 15 parts. All parts have some features that are either difficult or impossible to be made by traditional methods. These features are characterized by light weight, structural integrity, and cost savings.
Edwin Joffrey Courtial
ICBMS, Claude Bernard University Lyon 1, France
Title: Yield stress agent for silicone 3D printing

Biography:
Edwin-Joffrey Courtial has completed his PhD from IMP (Ingénierie des Matériaux Polymères) lab, Université Claude Bernard Lyon 1. He is a researcher specialized in materials science and rheological behaviors, and working in ICBMS lab, Lyon, France, inside the innovative platform 3D.FAB. These main activities are focus on correlation beetween (bio)materials formulations and rheological behaviors to define 3D (bio)printable conditions.
Â
Abstract:
3D printing deposition technology allows surgeons to produce patient-specific implants with high degree of effectiveness. However, biomimetic properties (mechanical behavior) of implants can only be obtain with silicone elastomers which are some of the most challenging materials to be 3D printed.
Rheological behavior, particularly yield stress character1, of viscoelastic materials is well known to be the key parameter to successfully use 3D deposition technology. Thus, if the stress reach a high enough value, the shape of printed object is holded during and after deposition, but also during post-printing polymerization process. Unfortunately, the yield stress properties of high
viscosity silicone is often too low to permit efficient 3D printing. Addition of yield stress agents in silicone formulations might be a solution to this problem and silica2 or glass fiber3 are commonly used in silicone formulations to change rheological properties. However, the presence of these charges implies modifications of the final mechanical properties of the silicone related to the high rigidity of the added charges. The consequence here is then the production of 3D objects with poor biomimetic behavior.
We are here proposing the use of polyethylene glycol (PEG) as low rigidity, yield stress enhancer charge, to be used with high viscosity silicone formulations, as a breakthrough toward silicone biomimetic implants 3D printing. This charge interacts with the surface of the silica dispersed in silicone formulation through hydrogen bonds. A secondary network is then created which provides a strong enough yield stress character, leading to efficient 3D printing capability (Figure 1-2). The low energy of this network unchange the initial mechanical properties of silicone after curing.
Clear experimental results will be presented together with case study of highly challenging 3D printing, demonstrating the superiority of the approach.
Jia Min Wu
Huazhong University of Science and Technology, China
Title: Research progress in additive manufacturing of ceramics and some related applications

Biography:
Jia-Min Wu has completed his PhD from Huazhong University of Science and Technology. He has been in charge of more than 10 research projects in China. So far, Dr. Wu has published more than 30 academic papers in Journal of the European Ceramic Society, Journal of the American Ceramic Society and other top journals on ceramic materials. Meanwhile, he has applied for more than 20 patents in China. In addition, Dr. Wu has also acted as reviewer for many ceramic related repute journals, and he has been invited to give speeches in several international conferences on additive manufactruing of ceramics.
Abstract:
Compared with traditional methods, additive manufacturing (AM) technology has shown great advantages in preparing high-performance polymer and metal parts with complex shape. However, it is difficult to prepare high-performance ceramic parts with complex shape by AM technology. So far, Prof. Shi Yu-Sheng’s group in Huazhong University of Science and Technology has done many researches on the preparation of various ceramic materials via Selective Laser Sintering (SLS) and Stereo Lithography Apparatus (SLA). Regarding SLS, three methods, namely mechanical mixing, solvent evaporation and dissolution-precipitation, were used to prepare ceramic-polymer composite powders with good fluidity. Subsequently, porous cordierite, kaolin and Si3N4 ceramic parts with high porosity were prepared by SLS. In order to acquire dense ceramic parts, Cold Isostatic Pressing (CIP) process was used to densify the SLSed green parts, and Al2O3, ZrO2 and SiC ceramic parts with high density and complex shape were successfully prepared by the SLS/CIP hybrid technology. In the recent research of Prof. Shi’s group, dense Al2O3 and ZrO2 ceramic parts with high density and high precision were prepared by Stereo Lithography Apparatus (SLA), in which the raw materials and AM equipment were all developed independently by Prof. Shi’s group. On the basis of above researches, the SLS and SLA technologies were used to prepare high-performance ceramic parts in the application of ceramic dental restoration, honeycomb ceramics, etc.
Sonke Steenhusen
Fraunhofer Institute for Silicate Research ISC, Germany
Title: Two-photon polymerization: A femtosecond laser-based technology for additive manufacturing in life sciences and microoptics

Biography:
Sönke Steenhusen studied physics in Würzburg and joined Fraunhofer ISC in late 2007 beginning his work in the field of additive manufacturing. At Fraunhofer ISC he developed machines for two- photon polymerization and investigated the 3D patterning of hybrid polymers for applications in microoptics. He is (co-)author of several papers in the field of 3D lithography. Currently his position is deputy head of the “Optics and Electronics“ department at Fraunhofer ISC, which is dedicated to the development and processing of novel materials for optical and electronic applications.
Abstract:
3D printing has been widely adopted on the macroscopic domain not only for rapid prototyping but also in manufacturing. Several technologies ranging from the consumer market to an industrial level have been established. However, on the micron-scale the possibilities to go into the third dimension are limited as the voxel sizes are dominated either by the diameter of particles in powder-based additive manufacturing, by the thickness of the filaments, or the diameter of the droplets in inkjet printing.
These constraints can be circumvented when using femtosecond laser-based photopolymerization in liquid photopolymers for creating 3D microstructures. Here, the solidification of the material is strongly confined to the focal spot of focused laser pulses where the intensities are sufficiently high to trigger two-photon absorption. Hence, two-photon polymerization is an inherent 3D technology with voxel sizes down to 100 nm. The exposure strategy is similar as in conventional 3D printing. The volume to be written is scanned in 3D, typically in a layerwise fashion. As in UV-lithography a subsequent solvent wash (development step) is needed to get rid of the unexposed, and still liquid, resin.
We will demonstrate representative application examples from different fields of research. In life sciences 2PP-written 3D structures can be used as substrates for cell cultivation, as they mimic the natural, porous environment which is required for proper cell expression. On the other hand, 2PP can be used for diffractive and refractive microoptical elements which reveal excellent surface quality and directly benefit from the freedom in design which only 3D printing can offer.
Teresa Russo
National Research Council, Italy
Title: 3D Printing and nanocomposite gels as a new challenge in tissue repair and regeneration

Biography:
Teresa Russo obtained a PhD in Materials and Structures Engineering (Biomaterials) at the University of Naples, Italy. She is as a researcher of the Institute of Polymers, Composites and Biomaterials (IPCB) – National Research Council of Italy – and her work is mainly focused on the possibility to combine Additive Manufacturing technologies, electrofluidodynamic techniques and multifunctional injectable gels for the optimization of multifunctional devices for tissue repair and regeneration. She is currently author of national and international papers, different book chapter and communications in international and national conferences. She has also been serving as an editorial board member of repute journals.
Abstract:
Over the past years, polymer-based materials have attracted research interest in the field of tissue repair and regeneration. Porous bioactive scaffolds with controlled properties can be obtained by processing polymer-based materials, as “solids” or injectable formulations.
Design and applications of injectable systems and hydrogel-based composites able to promote the regeneration of soft tissues, trying to reduce surgical invasiveness and to enhance efficient biomolecular interactions with cells, is a crucial aspect for damaged tissue repair. Furthermore, in order to repair bone, cartilage, intervertebral disc, adipose tissue, neural, and cardiac tissue, hydrogel-based materials have been widely analyzed as cell delivery systems providing a controlled release of drugs, proteins, cells, gene and other immobilized biomolecules. The suitable combination of 3D scaffold with hydrogels can provide high performance and functional systems, also focusing the attention on the possibility to control drugs or bioactive agent release.
In this scenario, 3D polymeric and composite rapid prototyped scaffolds were properly designed and developed, by means of rapid prototyping technique.
Furthermore, different formulation of collagen and collagen-low molecular weight hyaluronic acid (LMWHA) were selected and combined with 3D scaffolds.
Micro-computed tomography and compression tests were performed in order to analyze the morphological features and mechanical performances of 3D structures, respectively.
On the other hand, rheological and injectability tests were performed in order to obtain important information on the functional properties of the injectable systems in terms of viscoelasticity and flow behavior.
Biological analyses have also highlighted interesting information on cell-material interaction.
Daniel S Engstrom
Loughborough University, UK
Title: Additive manufacturing of metal-ceramic metamaterials for RF communications

Biography:
Daniel S. Engstrøm has completed his PhD from the Technical University of Denmark (DTU), followed by post doctoral positions at Imperial College London, University College London and University of Oxford. He has been a lecturer in Additive Manufacturing since 2015 at the Wolfson School of Mechanical, Electrical and Manufacturing Engineering at Loughborough University as part of the Additive Manufacturing Research Group (AMRG).
Abstract:
Metamaterials is a class of engineered materials with properties not found in nature. For Radio frequency (RF) communicatons these materials are envisaged to be used for planar antennas and RF devices where advantages are obtained by engineering the permitivity and permeability of the composite structure. Metamaterials for RF communications include those comprising of sub-wavelength highly ordered arrays of conductive materials embedded in a dielectric host material. Metals are the obvious choice for the conductive part and ceramics offer a high permitivity and low loss dielectric host medium. Additive manufacturing (AM) enables remarkable flexibility in the level of geometric complexity and lends itself well to the manufacturing of 3D metamaterials. Although AM of metals is well established, AM of combined metal-ceramic is still only at the research stage. Especially the high sintering temperatures required for ceramic manufacturing makes the process non-compatible with metals. In this project we use a dispensing system and localized laser processing to manufacture metamaterials. The project is part the EPSRC Grand Challenge; SYMETA – SYnthesizing 3D METAmaterials for RF, microwave and THz applications (EP/N010493/1).